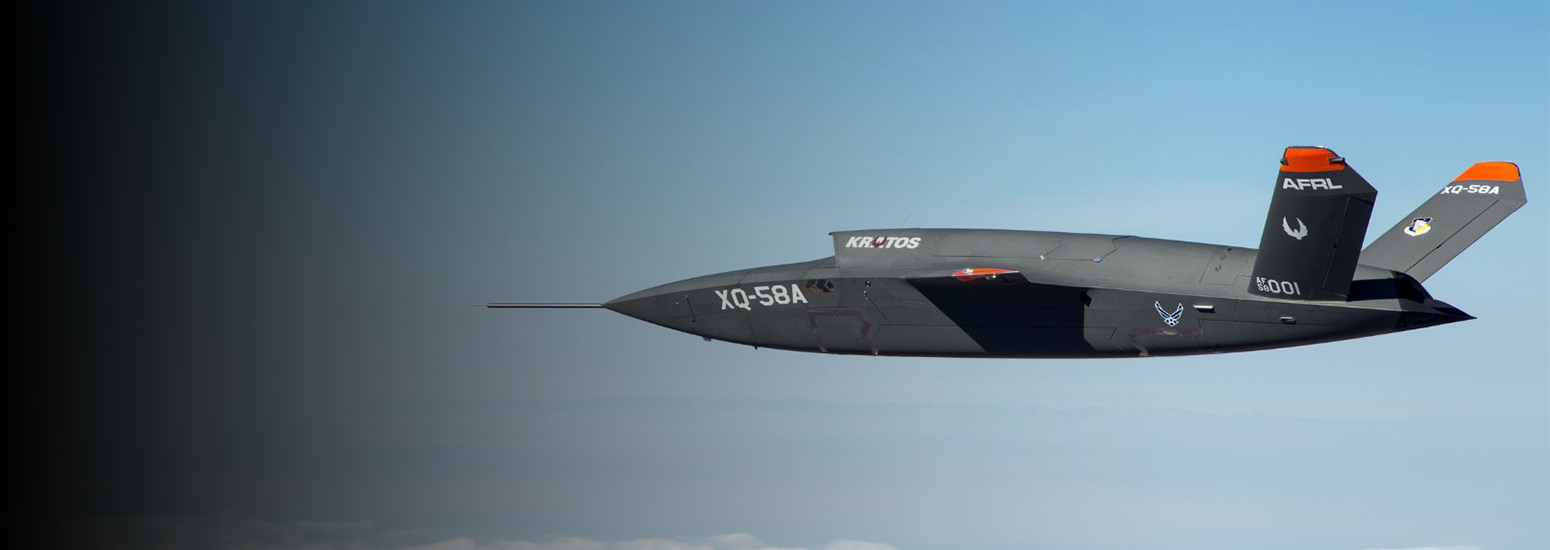
Air
Operating for decades, Kratos is a world leader in designing and engineering jet-powered, high-performance unmanned aerial vehicles (UAVs), avionics, and mission systems. Kratos also delivers approved target systems for the Patriot surface-to-air missile system and high-performance systems for the U.S. Army, Navy, and Air Force, as well as our international allies.

Join the Kratos Team
Kratos engineers and deploys technology and systems that move national security forward, with the cost, speed, and reliability that make readiness certain.
Join us—explore open roles and apply today.
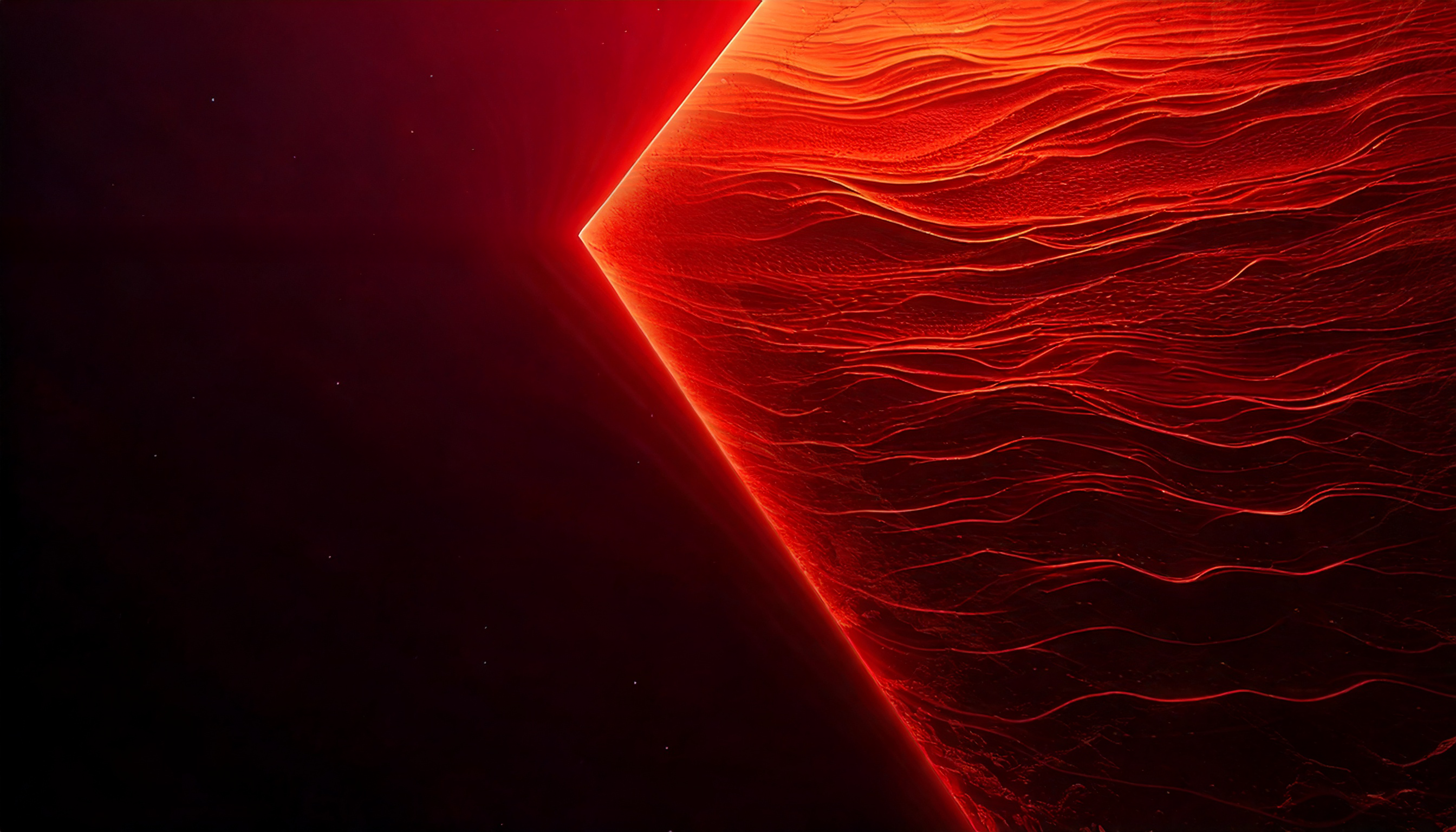
Contact Us
Have questions or want to learn more about Kratos and our innovative solutions for national security? Fill out this form.
Thank you. We will use your information to respond to your inquiry. We may also contact you about our products and services. You may opt-out at any time using the unsubscribe link in messages you receive from us. You can learn more about how we handle your personal data and your rights by reviewing our privacy policy.